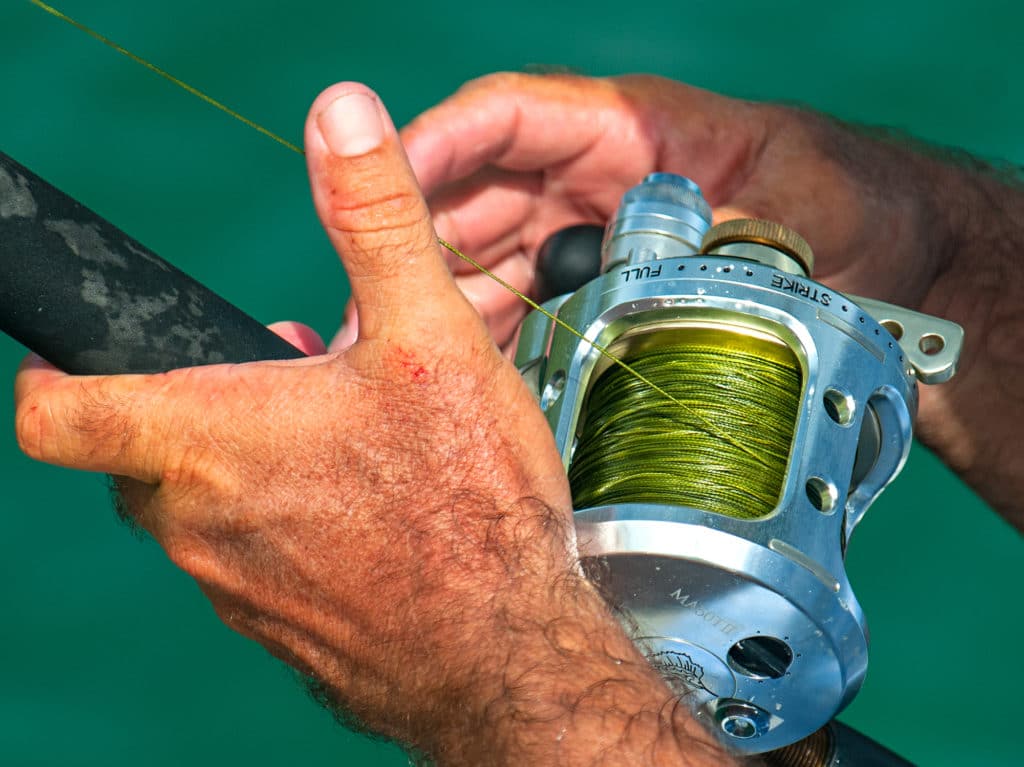
Inside the toughest reels that anglers rely on for their most strenuous fights are key mechanisms that don’t receive much attention: gears. Fishermen are quick to consider drag settings, bearings, line capacity and even gear ratios, but ignore details such as gear material and gear cut.
The toothy, circular components determine how strongly and smoothly a reel turns, especially under strain in drawn-out battles. Lesser gears can feel like a wind-up toy, while superior gearing feels and acts more like a winch.
A reel’s price is a strong indicator of what to expect from the gearing, but I wanted to know more. I asked top reel manufacturers about tooth cut, material, longevity and gear size. Some top companies were quick to protect their proprietary manufacturing processes, but others divulged more, providing an informative dive into conventional and spinning gears.
Material Goods
Gear materials can range from brass, zinc and aluminum to stainless, but for maximum strength and durability in saltwater conditions, stainless-steel drive gears and pinion gears are often the top options. Penn uses stainless on all its higher-end conventional lever-drag reels, such as the Internationals and Torques, says Penn senior product manager Mike Rice. “In most cases we use stainless steel for the pinion main gears,” he says, “but we prefer to heat-treat the pinion gears to increase the hardness.”
Zebco Brands uses stainless steel in all heavy Fin-Nor trolling reels, VS and VSB Van Staal reels, and Quantum Cabo offshore spinners because it is strong and durable, says Chris Littau, fishing manager of Zebco Brands. “But stainless is also expensive and difficult to make smooth,” he adds.
Different reel manufacturers utilize different types of stainless. For example, Accurate uses 303 stainless steel; Alutecnos, 316 stainless; and Okuma, 17-4 stainless. Manufacturers may use different stainless alloys, or combinations of metals, dependent on the reel, but they try to keep the same alloys inside a specific reel to prevent electrolysis caused by dissimilar metals.
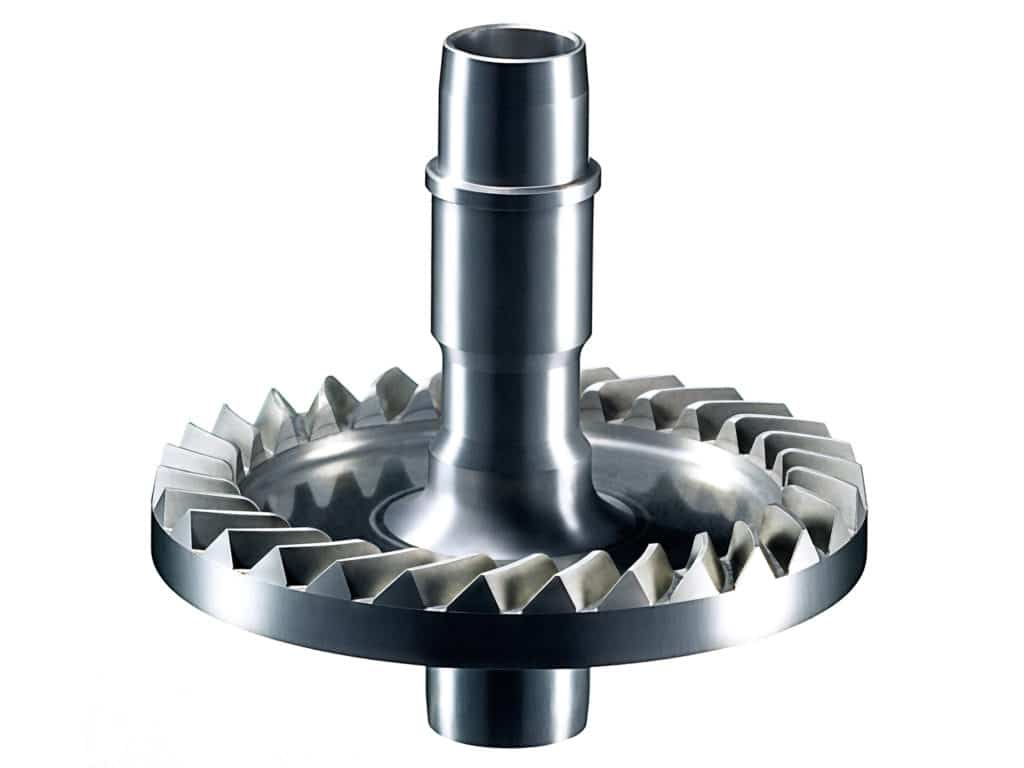
The different types of stainless can be confusing, but understand that each number helps explain the alloy’s unique makeup. “I think it’s important to point out that all engineered, industrial-grade metal materials are alloys,” says Littau. “I have heard people refer to an alloy as a cheap material, but in fact most pure materials are mostly useless without being alloyed.”
Stainless steel in the 300s, such as 303, 304 or 316, cannot be hardened by heat — hence the use of cold forging. Stainless 17-4 can be molded via heat treatment. In the fishing community, stainless 304 is recognized for its corrosion resistance, while 17-4 is known for its hardness — still, most different types of steel can exhibit similar characteristics at different levels.
“The 17-4-grade stainless steel is known for its high strength and ability to withstand high temperatures far exceeding what a fishing reel can generate,” says John Bretza, director of product development at Okuma Fishing Tackle. “It gives us the strongest grade of material we can use and still have the corrosion resistance needed. It also gives us the ability to heat-treat, depending on our target application and desired hardness.”
For spinning reels, Shimano uses a cold-forged aluminum Hagane gear in its new Twin Power SW and Stradic models. “Aluminum is lighter than brass,” points out Chris Hess, a senior manager of product planning at Shimano. “The precision of our dies and expertise in the cold-forging process allow us to create a gear with incredible strength, durability and smoothness.”
In total, manufacturers utilize stainless and other alloys to create ideal shape, strength and durability in their gears to fit the exact needs of each reel.
The Cut and Process
Have lever-drag reels advanced past traditional gear teeth, often called straight-cut? Penn has used the same gear cut for decades, using a lower pitch (teeth-per-inch ratio) because of its strength. Manufacturers such as Accurate also believe standard gear cuts are still an invaluable option.
“Our gears are cut on CNC hobbers and shapers,” says Ben Secrest, vice president of sales and marketing at Accurate Fishing Products. “We believe this is the best way to achieve a consistent, smooth, precise gear; plus we’re able to control tolerances and accuracy. Our spur gears are designed for direct power and torque.”
Daiwa and Alutecnos are not as open about their gear manufacturing processes, but both divulged that they cut their own gears using proprietary methods. Daiwa calls its gear-cutting process Digigear, or Digital Gear Design. For Alutecnos, each gear is robotically lathed at the TMB (their parent company) Italian factory, which also machines gears for ZF (an automotive supplier) and other brands, says Alutecnos’ U.S. manager Mason Featherston.
“Van Staal gears are machine-cut spiral bevel gears, just like the rear end of a truck,” says Littau. “They are expensive to manufacture and make smooth, but will last a lifetime.”
Shimano spinning drive-gear teeth are not cut, but instead fashioned through the cold-forging process: Precision gear teeth are constructed down to a micron level with one stamp of the cold-forge press. Hess believes that machine-cut gears are initially smooth, but over time can wear down faster and become rough under heavy loads.
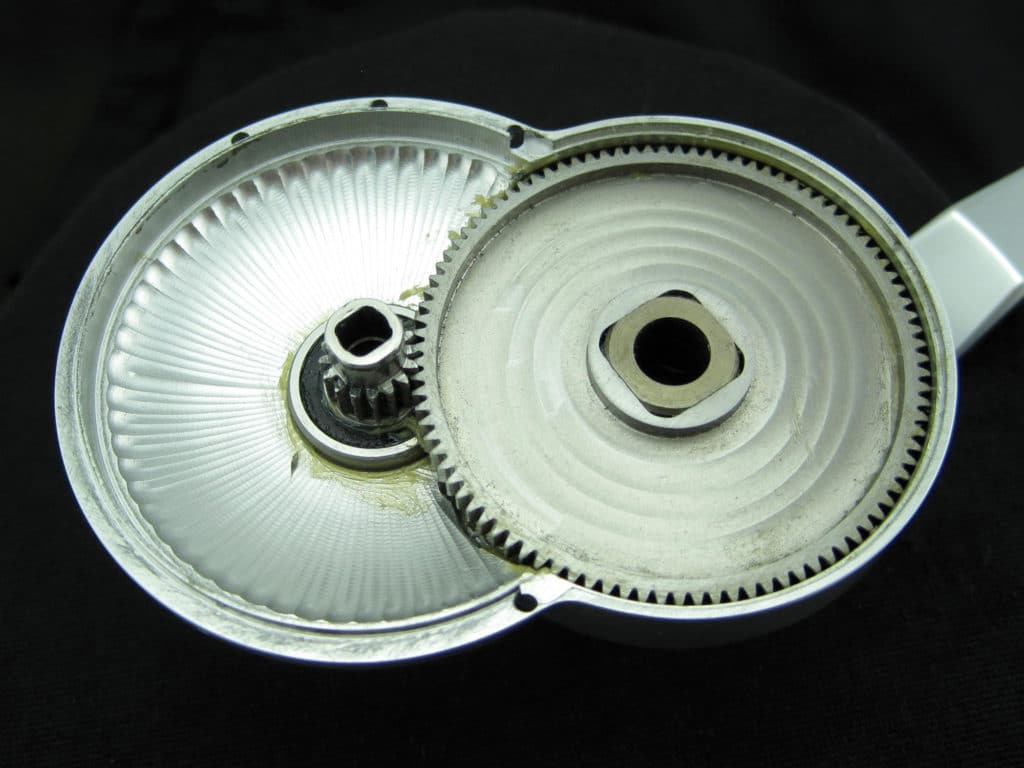
“If you open most reels and look at the engagement between the pinion and drive gear, you will typically see two gear teeth engaged,” says Hess. “While these teeth offer good durability, there can be some ‘play’ between them, which can create a rough feeling.” To overcome this, Shimano has begun to use micro-module gear teeth. By making the gear-teeth module smaller, Shimano was able to eliminate a lot of the play and create a smoother-feeling gear through increased tooth engagement.
With the Makaira series, Okuma set out to create a silent-retrieve big-game reel, so the company opted for helical-cut gears. Helical-cut (or spiral-cut) gears have more teeth meshing at any given time, translating into greater load-bearing surface area and more gear-tooth engagement between the main gear and the pinion gear, says Bretza.
“Helical gears are so strong that they can create axial loads that overpower other components, which is why our reel was built from the ground up around this system, to make sure that all the strength and pressure loads work together,” says Bretza. “It’s why other companies don’t simply retrofit their reels with helical-cut gears.”
More Than One Size
Gear ratio has a meaningful impact on gear smoothness in fishing reels.
“Early on, anglers converting standard-gear-ratio reels to high speed would lose power,” says Bretza. “The problem was that they kept the same-diameter gear and added more teeth to accomplish a higher gear ratio.”
The gear teeth were smaller in size, which reduced pulling power, torque and overall durability. Today, modern reels often have drop-down gear boxes, offset from the frame to allow more room for larger gearing.

“In terms of size and strength, a thicker face width of the gear [creates] a stronger gear because you’re able to distribute the load over a wider area,” says Rice. “Unfortunately this adds weight, so there’s always a necessary compromise.”
The size of the gears greatly affects toughness, which is why many reel manufacturers utilize oversize gears for increased power, especially on higher-speed reels.
“Manufacturers today increase the overall diameter of their gears so they can create a high-speed reel with appropriate-size gear teeth to keep durability and muscle in the gears,” says Bretza.
A lower gear ratio will always be the most durable when it comes to force and smoothness, but modern manufacturers are finding ways to develop higher-speed reels that still have good amounts of the same attributes.
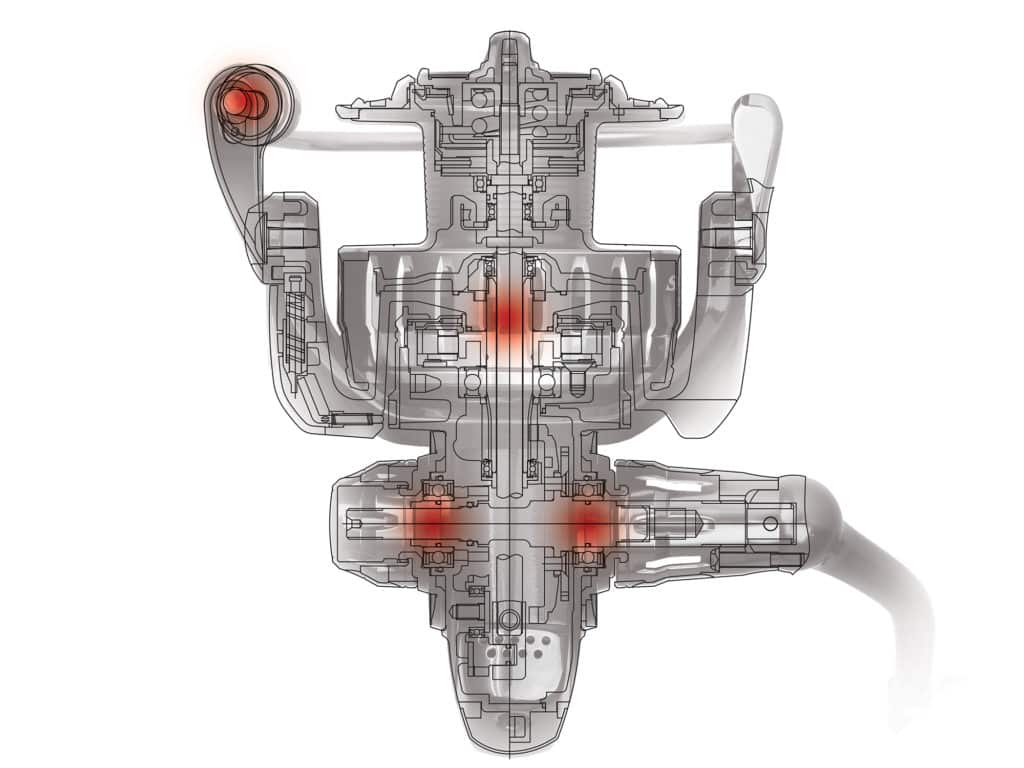
Reel Longevity
The best way to prolong the life of your reels is to do an annual check to see that your gears are properly lubed with the correct type and amount of grease. Taking them to a trusted tackle shop is a good option. The grease helps reduce friction and control heat buildup in your reel.
“Stainless-steel material gives gears longevity under normal fishing conditions,” says Accurate’s Ben Secrest. “The gears can last a lifetime. Softer metals can be warped when fished outside the intended design.”
Even still, corrosion is a constant struggle with saltwater gear. Daiwa figured out a new way to prevent salt intrusion in the bearings and gear box.
Daiwa’s Mag Seal technology uses a thin film of magnetic oil to keep salt water, dust and grit from entering the reel’s rotor bearing and gearing, says Curt Arakawa, Daiwa’s marketing manager. “Magnetic oil is one of a new generation of nanofluids that can change density and shape when a magnetic field is applied,” he says. “This method offers substantially less winding friction than would an ordinary rubber seal.”
Daiwa’s new Exist spinning reels feature Mag Sealed ball bearings on both sides of the drive gear, in addition to a Mag Sealed main shaft and line roller for trouble-free rotation and less maintenance in harsh saltwater conditions. Mag Seal is also used in the new Saltiga series to prevent water intrusion between the reel’s rotor and body.